Padding uses a special glue to allow multipart forms or cut sheets to be attached to a chipboard backing, keeping them together as a single unit called a pad. Both cut sheet forms and unit sets can be padded. Cut sheets may be pulled off one at a time and unit sets can be removed as a set from the pad.
To pad forms, they are divided into units, typically 25,50, or 100 forms to a unit. Chipboard is placed at the end of each unit. The forms are stacked on a padding press and pressure is applied to the edge to be glued. Padding adhesive is spread uniformly over the end of the forms to be padded. When the padding compound is dry, the pads are cut apart at the chipboard that divides each unit. (See the animation below to visualize the process.)
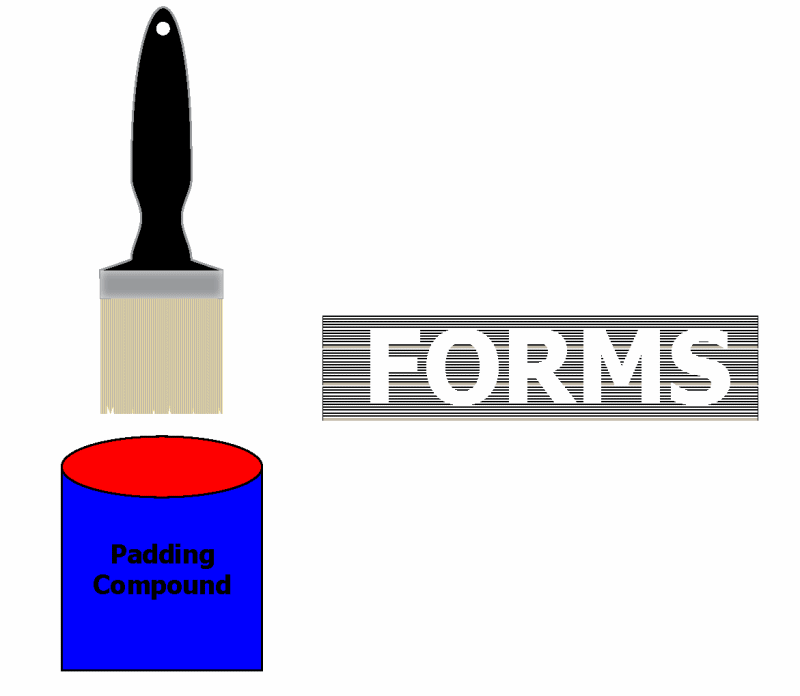
There are also various machines that can be utilized to automate the process. These machines typically are loaded by hand one set at a time. A button or foot pedal is pushed and the machine clamps the set together and runs it through a cycle that includes hot melt adhesive and quick drying. A pad can be produced in as little as three seconds with an hourly total of up to 3400 pads an hour. See the image of our Brackett Padmaster below.
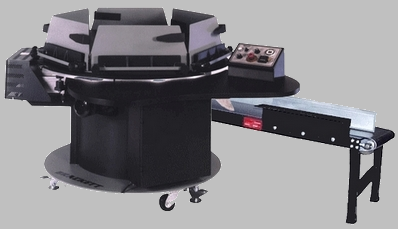
Brackett Rotary Padding Machine Web Page: Their page includes specifications and video of the machine in operation.